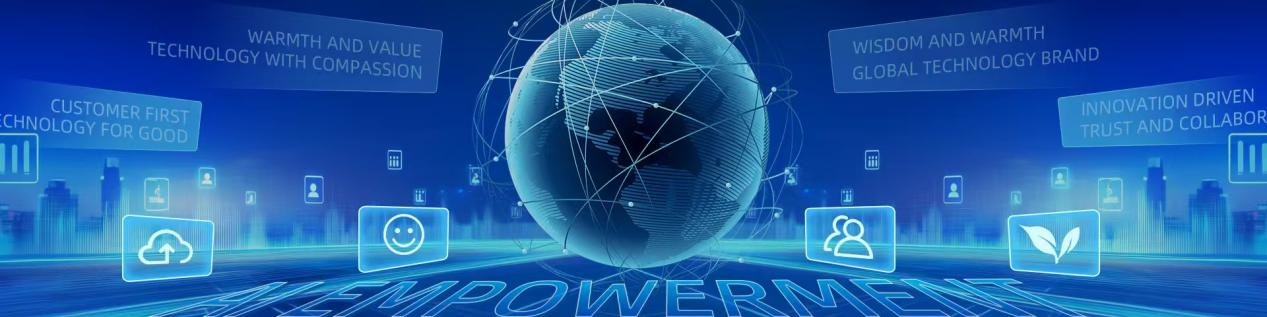
Testing Capabilities
Production Processes:
High-Volume Production:
DC-Powered Cameras: Produces 800–1000 units per line daily (25 days), supported by 18 workers.
Battery-Powered Cameras: Produces 700–900 units per line daily, requiring 40 workers.
Advanced Assembly and Testing Workflow:
Products are precisely positioned using specialized fixtures.
Cameras undergo activation and sleep mode cycles to simulate real-world operation.
Heat source calibration simulates human body temperature to trigger activation, ensuring functionality under realistic scenarios.
Signal attenuation testing involves placing the product 150 meters away, checking its operational stability and signal integrity under simulated conditions.
Quality Assurance Testing:
Environmental and Functional Testing:
Simulates real-world heat and positioning conditions to ensure product activation and performance consistency.
Comprehensive power dissipation testing is monitored using advanced equipment like the Monsoon Power Monitor AAA10F.
Reliability and Durability Testing:
Products are subjected to multiple trigger and activation scenarios to evaluate robustness.
Long-distance signal attenuation testing ensures operational efficiency under challenging conditions.
Specialized Testing Equipment:
Use of advanced power monitors and high-precision heat source simulators to test and optimize operational parameters.
Equipment and methods adhere to strict industry standards to maintain consistency, reliability, and quality.